Customer Profile
Industry: Construction/Civil Engineering
Application: Monitoring Transportation Infrastructure

About Gruppo Centro Nord
This project came about through our participation in the Elis and Foundation Open Factory initiative. This is one that facilitates innovative incentives between companies deemed as mutually beneficial.
Gruppo Centro Nord is a construction company that specializes in creating prefabricated concrete structures that support the cities around us. Founded in 1964, the company takes pride in creating structures that respect the spaces they occupy, rather than imposing on them.
Gruppo Centro Nord believes in grafting together various elements to reflect the quality of the units that constitute their buildings. They value tradition and maintain a future-first approach, aiming to create industrial manufacturing processes that meet the changing needs of their clients.
Using prefabricated concrete modules in construction has proven to be environmentally and financially sustainable. Gruppo Centro Nord manufactures the modules offsite and delivers them to the construction site, where they are slotted together to create the final infrastructure. If needed, elements like insulation are built-in and do not need to be inserted later. This means that building time is shortened, resulting in lower labor costs.
Prefabrication also lowers the environmental impact of construction as it allows the use of scrap metals and other recycled materials. In addition to this, prefabrication reduces the amount of waste and emissions, thanks to precise measurements and quality control.
The Challenges
This Proof of Concept (PoC) sought to perform continuous monitoring of infrastructural degradation to predict, and consequently, avoid triggering phenomena that would accelerate deterioration. Monitoring would be done by attaching sensors to the modules to identify and evaluate these events.
The proposed solution would be a giant step towards innovation in construction, allowing us to monitor the long-term performance of prefabricated structures from the time of installation. Gruppo Centro Nord chose to partner with 221e based on our innovative solutions that merge IMUs with sensor fusion and edge AI.
One of the hurdles was determining how to successfully integrate external devices (sensors) with the prefabricated modules. This was an unprecedented undertaking, and there was the risk that the sensors would not operate as they should upon installation. Determining the correct placement of sensors was central to the collection of accurate data that would lead to the development of the evaluation tool. Failure to do so would prove detrimental to the progression of the project.
Connectivity also had to be considered and planned for carefully. The nature of the PoC meant that the sensor location was not easily accessible (being located on a busy motorway). Data collection would have to be simplified and would rely heavily on IoT connectivity and data logging optimization.
Our Solution
The Muse sensor system was selected as the ideal solution per Gruppo Centro Nord’s request for a sensor system that would operate as a reliable monitoring device for their prefabrications. Muse was developed for such applications, possessing the inertial sensors necessary for collecting data relevant to the project. The hardware was crafted for robustness and allows it to function accurately under the harsh and varying ambient conditions that concrete infrastructures endure.
The advanced Muse miniaturized sensor systems would be mounted on prefabricated elements that form the high-speed train’s tunnel, located below a section of the motorway.
The 221e engineers chose to install the sensors in three key locations: one at each end and the central underside of the bridge deck. The mid-section of the bridge deck bears most of the load and so experiences the brunt of the structural stress (being the furthest point from the supporting columns). It was determined that these locations would offer accurate measurements regarding the conditions under which the structure was operating.
The data analysis focused on accurately characterizing the phenomena that occur during normal functioning of the bridge, particularly in terms of vibrations and event detection strategies. This would later provide tools and indicators that could signal the health of the infrastructure.
Signal processing was implemented through the following strategies:
- Inertial data compensation was performed with respect to the device orientation, to render the data recorded from different devices comparable and referred to the same frame (i.e., absolute reference frame).
- Event detection, exploiting acceleration data only. Vibrations generated by the transit of vehicles on the motorway are analyzed. Vibration events can be classified in terms of different intensities. They are used to perform a statistical evaluation of the traffic conditions, as well as monitor the frequency of infrastructure use and displacements.
- Evaluation of sensor positioning: The sensors were installed in three separate locations. The aim here was to evaluate the impact of sensor positioning on the structure concerning the data quality and event detection performance.
- Frequency study: Analysis performed on the frequency domain identifies characteristic vibrational frequencies of the infrastructure and potential anomalies over time.
- Ambient sensor data are used to identify extreme or abnormal environmental conditions and determine the effects of long-term exposure on the deterioration of the structure.
Results
A joint analysis between Gruppo Centro Nord and 221e was performed to identify which data would be most advantageous when developing an infrastructure monitoring tool.
This project led to a prototype for a measurement, and monitoring tool capable of event detection, indicating events that may result in a faster rate of structural deterioration, and identifying high-stress areas within infrastructure. It reduces the need for human intervention and can be run on an extended basis. The installation of the sensors is not an invasive process and can be done during manufacture so as not to disrupt the structure post-manufacturing.
A solution like this ensures a higher level of security by merging intelligence, hardware, and an interface to monitor infrastructure. It can be applied to other Gruppo Centro Nord works in the planning phase, offering its customers a high-quality product with added value.
Conclusion
This PoC paves the way for intelligent sensors to be applied in tunnels and overpasses for constant monitoring of structural degradation. The result would be more efficient and accurate operations management, as well as data-driven insights for better maintenance practices.
This non-disruptive, smart engineering solution could be applied in a wider context, standing in line with Gruppo Centro Nord’s culture of innovation. It would be a significant step towards our transition to smart cities for buildings that are monitored continually for structural integrity and more secure road networks.
This technology would shift Gruppo Centro Nord’s standing from “manufacturers of prefabricated concrete structures” to “producers of intelligent prefabricated concrete structures”, further distinguishing them from their competitors. It is a field that holds a lot of promise, as such structures that integrate intelligence are offered in a limited capacity on the civil engineering market.
“We chose to partner with 221e because of their expertise in sensors and data analytics with edge AI techniques. The work carried out highlighted interesting parameters that can be monitored and used through the application of sensors and the integration with IoT technologies. These innovations are becoming pervasive and will play a key role in the near future to increase the safety and efficiency of our infrastructures, both in terms of smart cities and in transport. The 221e team proffered its expertise and collaborative spirit, giving us the opportunity to explore these new technologies.”
Arturo Marconi – Technical Director
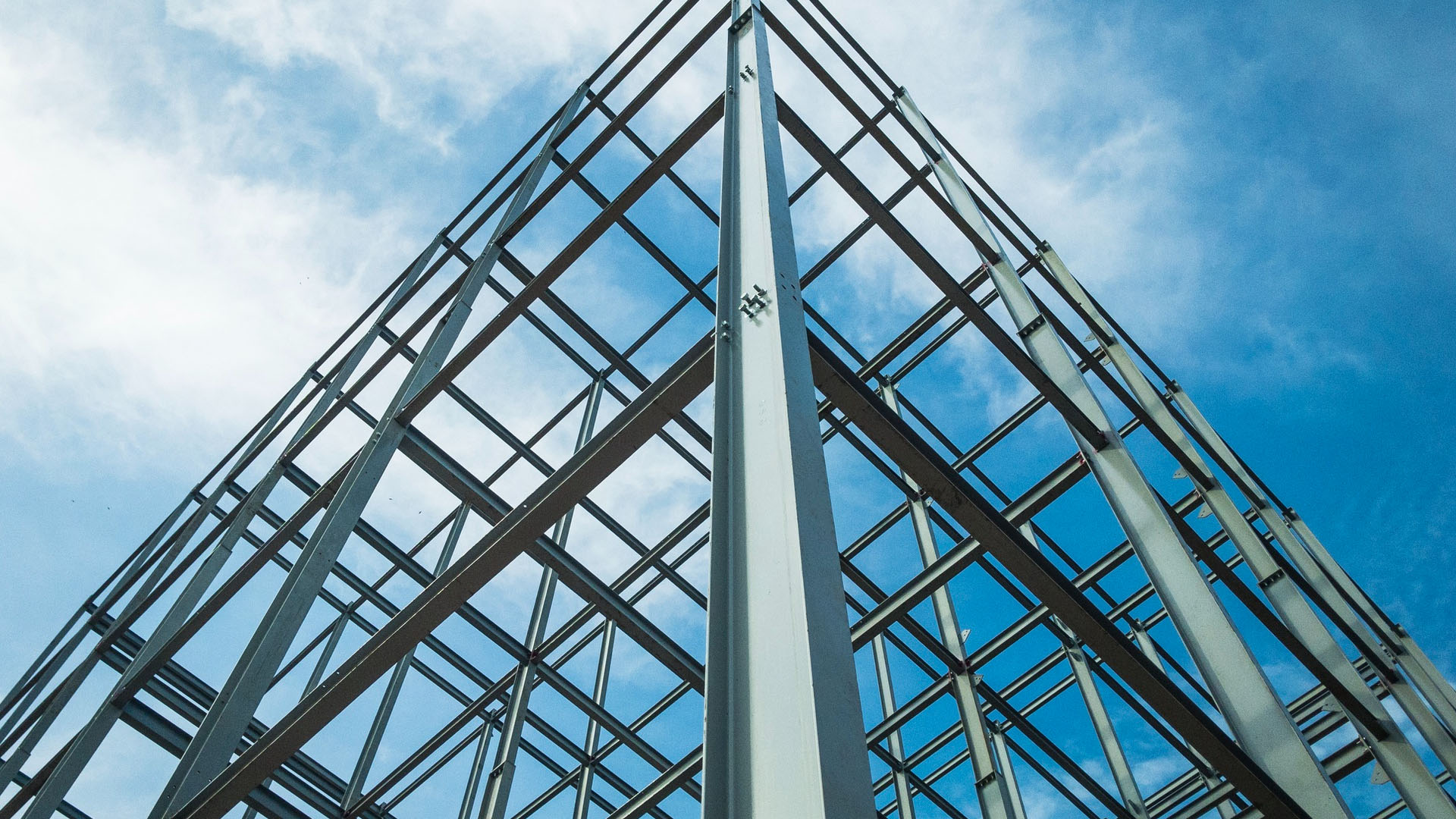